The history of Verket
Historical background
The explosive industrial development worldwide placed new demands that the small, craft-driven works in Sweden could not meet. To operate a works, regulated water power, large-scale operations, and efficient transportation systems were required.
In 1872, Hjalmar Petre and Hampus August Cornelius purchased Stora Kopparbergs Avesta Works with the associated waterfalls and properties. In 1873, they formed Avesta-Garpenberg AB, with Cornelius as CEO and plant manager. At the site, there were buildings from the closed copperworks as well as a smaller bar iron forge. The company was not interested in the old buildings and immediately began planning and constructing the new large ironworks.
It was a period of economic prosperity when the new ironworks was established, and the calculations were based on continued high revenues. In 1878, Sweden underwent a financial crisis, which was a direct result of large investments made in areas that could not provide profitability within a reasonable time. In 1879, Avesta-Garpenberg AB went bankrupt. After the bankruptcy, Cornelius was appointed to continue overseeing the operations under the new owners, Jernkontoret and Norrköpings Enskilda Bank. In 1883, Avesta Jernverk AB was founded with Jernkontoret as the majority shareholder. One of the minority shareholders at that time was Axel Johnson. In 1905, Axel Johnson acquired the majority of shares, and from 1910, the ironworks became entirely Johnson-owned.
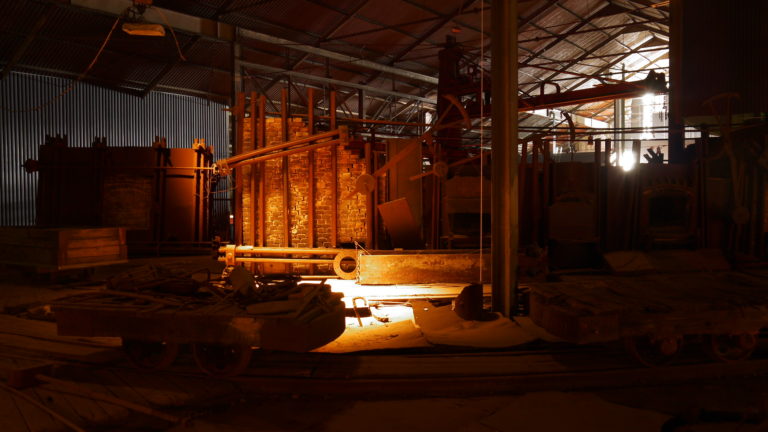
Detailed History
Great industrial conditions
Cornelius is the driving force behind management, behind the first phase of the development of the ironworks. He understands that if one is to run a large-scale modern business, one must be involved in influencing the development of society in the direction that is good for the business.
An important development phase in the infrastructure was the railway. In addition to his task at the ironworks, Cornelius was also CEO of Southern Dalarnas Järnvägs AB in 1878 - 98. The railway Krylbo - Norberg was completed in 1874 and was a prerequisite for the ore transport to the cabin. In 1875, the Avesta - Krylbo stretch was completed, in 1881 the Avesta - Borlänge section was put into use.
Cornelius also took the initiative for the first telephone lines between Krylbo, Avesta, Fors, Garpenberg, Finnhyttan and Dormsjö, which were established in 1885.
To get over Storforsen, a highway bridge was built in 1891
Another important prerequisite for running modern industry is the energy supply. The channels built for the needs of the copper mill gave too little power. In 1881 - 83, the first large dam was built at Storforsen. The water was led into a newly built canal between the manor house and the cab and the development of turbine-driven works in the cabin took off. The first power station at the cabin was completed in 1898. The current power plant building at Storforsen came to 19
The new company invested in large-scale operations. The blast furnaces were considerably larger than the older ones. All the new technology needed to improve the results was also accepted. Future companies continued to build on the same tradition, namely to invest large and best technology. To achieve these results, well-known engineers were hired. As a designer and builder of the new ironworks, Albert Bergström, 1873-1884, was hired. Henrik Tholander, 1875-1892, employed as cabin engineer and metallurgist. The investments made Avesta Jernverk grow into a large industry.
Society's development
During the time of the copper era, the people of Sweden and its traders were governed by various government regulations and regulations. During the 19th century, these disappear one by one. When the new ironworks are built, the business is not governed by anything other than internally determined decisions. This was something the workers had difficulty understanding. The life one lived during the time of copper use was so strongly bound to the mill and the benefits this entailed. For the utility workers, for example, it was stated that housing would be accessed through the mill. The new management did not oppose this, but made sure that the workers got housing equipped with new modernities gradually. Seen from a national perspective, it took a long time before Avesta developed as a modern society. The forms around the old mill community lived well into the 20th century.
Just as in the old mill, the workers continued to keep animals and grow to house needs. In the early 1900s, the new society grew outside the old village. A development that was accelerated by the management who needed housing for the growing workforce. The old pastures are filled with houses and streets. The old border, when the village and the bridge constituted a unit, is blurred in the new society, but remains in the minds of people. The workers are pulling down on their animal husbandry but right up to the 1940s it was common with household pigs. The company wants Avesta to become a modern society so that the dwellings in the old village are rusted and the first lawns are laid there, but they were few at the beginning for the residents wanted to continue cultivating. In the 1940s, there were plenty of potato fields in and around the village. A modernity that was drawn in both the ironworks and the city was electric light that came at the turn of the century 1900. Drinking water was taken from Storforsen before water and sewage were withdrawn in the 1930s. Water closet was installed in the 1940s. From that time, the workers at the ironworks begin to have access to special spaces for changing and washing. The canals were used for clothes washing into the 1940s. There were rock bridges where the women lay and lapped both summer and winter.
While the old mill society developed into a modern city society during the 20th century, other phenomena from the old mill life remained. When Axel Johnson died in 1910, the leadership was taken over by his son Axel Ax: son Johnson. The son was generally called "Consul General". The Consul General was very interested and committed to life in the village and the workers. The couple lived in Avesta Manor. The Consul General became like a utility. During anniversaries or major celebrations, the ironworks staff were invited to a party, and gifts were handed over to Christmas or during long-term illness. The Midsummer celebration was always organized by the work. The orchestra association and mill music year were other activities that were cherished by the Consul General. This commitment was appreciated by the people and characterized life in and around the ironworks. The old working spirit, the vi-feeling lived.
From Ore to steel
The ore arrived at the plant via the railway, from Norberg and Grängesberg's mining field.
A trestle track went in from the railway in a south-north direction over the ore plane. The wagons were emptied on the ore plane. Outside the south side of the rust oven building, there were pockets for quartz. Paths and quartz pockets were demolished in 1938.
Roasting furnace
In the roasting furnace, the iron ore was toasted. This was part of the preparation for the melting of the ore in the blast furnaces. During the roasting, sulfur is removed as gas and the ore kernels become brittle and easier to crush.
Both roasting furnaces are of Westman's construction. They are bricked with wrought iron reinforcements. The ovens were charged, refilled at the top, under the chimney. The ore was driven up from the ore plan, in ore dogs, wagons on ore paths demolished in 1938. The ovens were fired with blast furnace gas which was led via large pipelines from the blast furnaces to the ovens. The gas was then injected into the 16 gas hatches. There are spit doors over the gas hatches, and at the bottom 8 outlet openings where the roasted ore was rolled out. The roasting capacity was 45 tonnes per oven and 24 hours
In the roasting furnace building, rust burner base, rust burners, cab twists, ore slagers, lime slag, ore players, crushers and pushers worked.
The northern roasting furnace was completed in 1874, when the new business started.
The southern roasting furnace was built in 1883. There is a photo from 1883 where the southern furnace is newly built but not yet in use, the ore rail is missing
The ovens were taken out of service before 1938.
Sligrust ovens
In the shelter, the house is sintered.
Slig is mald ore, which, just like the remaining ore, arrived by rail to ore planes. From the ore plan, a dog lane went up to the ottoman that stood on the top floor of the rust house. Below the floor of the oven there are pockets for storing the finished sinter.
In Sligrostugnen, the coal and coal are mixed in a boiler with small holes in the bottom. The coal ignites and, through strong suction from below, the fire draws itself into the mass and warms so strongly that the sulfur is burned off. When burning, it is usually turned into lumps.
The Sligro rust oven had a capacity of 6 tons per day.
It was commissioned in 1917.
Sligrostugnen does not remain today
Ore base
The roasted ore was stored in ore bins awaiting further use. The ore contained varying amounts of silicon, etc., and therefore it was sorted into different bins.
The ore crusher
There is an ore crusher in a crusher pit beneath the floor of the Roasting Furnace Building. It was used for the ore destined for blast furnaces 1 and 2. It is a rotating stone crusher of the Gates model. The ore crusher crushed the roasted ore into nut-sized pieces. The crusher pit was open. The crusher was fed through a funnel-shaped upper part. The crushed ore comes out on the north side of the crusher, straight down into the ore chute standing on the track at the bottom of the crusher pit. Two people always worked at the crusher.
Drawings are available on rotating stone crushers from 1904 - 1924. Drawing B1301 "Rotating stone crusher" The ironworks collection, Avesta municipal archive.
The crusher was in operation until 1938.
Ore Games
With the skip car, the cart that stands down in the crush pit, the roasted and crushed ore was encouraged to the upper part of the blast furnace, the wreath. The ore was emptied there in ore pockets. Even the lime was run up with the skip car. The ore play was operated with turbine drive released by electric motor Drawing B533 Railway collection, Avesta municipality archive.
"Power to crushers, ore and coal hoists etc. was obtained from a turbine, which was placed where later the National Power Plant's first electric power station was erected" (W.Eriksson, Avesta Jernverk AB, part 1)
The game was started until 1938
Carbon track
Outside the cabin there were five large coal houses before. These were in a row in the south-north direction below the railway. They were demolished to leave room for the cold rolling mill that was built in 1939. The coal came via rail and was unloaded in the coal houses. Outside each coal house there was a turntable so that the carriages could be driven into the coal houses. The track lay on high bends, 2.5 - 5 meters up in the air. Each coal house held up to 80000hl of coal or coke. (Both 2nd and 1st blast furnaces have been fired with coke during certain periods). From the cabins a cable car went up to the blast furnace. The coal baskets were filled at the coal housings, driven up via the cable car and connected to the rail system found in the ceiling of the crane room. A coal basket held just over 5 hl. Drawing C298 The Ironworks Collection, Avesta Municipal Archive. Those who worked with replenishment of coal baskets were called carbon carriers and were led by carbonate bases.
The carbonl houses and cable car were demolished after the blast furnace operation was closed in 1938
Blast furnace
In the Blast furnaces, the ore was reduced with the carbon. In order to get the coal burned, hot air was blown in through the blast openings through the openings. At the bottom of the furnaces, liquid pig iron was formed
The pipes are bricks reinforced with wrought iron strips. They are all three 16.8 meters high. The ovens are of Tholander's construction. In Avesta, Tholander developed his idea with blast furnaces that are high and thin-walled.
Blast furnace No. 1, the southernmost, was built in 1874 and was taken out of service in 1938.
Blast furnace no. 2, middle, was built in 1876 and was taken out of operation in 1920.
Blast furnace No. 3, the northernmost, was built in 1915 and was taken out of service in 1918.
Everybody was occasionally dismissed from time to time.
The Blast furnaces were filled with ore, coal and lime at the top of the wreath. The set targets are closed, by Tholander's construction, ore and lime are filled in the outer ring, coal in the middle. Each set in Avesta consisted of approximately 420 kg of ore, about 15 hl of coal and about 95 kg of lime (according to the table of Swedish blast furnaces, from before 1915. Drawing B8, the Iron Works Collection Avesta municipal archive). The ore is rusted and crushed ore or sintered joint. The lime varied in amount depending on the silicon content in the ore. The number of sets varies, but the proportions between ore, charcoal and lime are about the same. Picture What happens chemically in the blast furnace
When the set goal was lifted to empty, it sparked a sparkle, like a fireworks display. In the ceiling there were large gaps over the blast furnaces. The sets were made 3-4 times per hour. The one who filled the ovens was called set-up.
In the lower part of the furnace, the temperature is about 1500°C. The iron melts and collects in the hearth of the furnace. On top of the molten iron floats the slag. To make the coal burn so fiercely that the temperature becomes high enough, heated air is blown into the lower part of the blast furnace through tuyeres, pipes that taper to a point inside the furnace. Slag was tapped from the furnaces in one direction and pig iron in another, with approximately six hours between taps if charcoal was used, and only a couple of hours between taps when coke was used. The slag could be cast into slag stones or poured out with water, cooling it so it broke apart and became granules. The pig iron was tapped into molds, pig beds, also called pig molds. Each blast furnace could produce about 10,000 tons of pig iron per year, but since one of them was always shut down, the total annual production was over 23,000 tons at most. According to the table mentioned above, blast furnace II produced between 21 and 26 tons of pig iron per day.
Those who worked in the raw house, the bottom floor of the blast furnace building, were masters, cab dredgers, slag hammers, slag drivers, and others. Additional services in their vicinity were railways, lubricants, couplers, sweepers
Blast furnace 1 was eventually rebuilt for heating with coke, which meant different proportions in the set-up. With coke, about 0.57kg of coke was used / 1kg of ore. The furnace became so hot from heating with coke that a cooling system with cold water was built outside the furnace. The process went faster, which is why the eliminations happened more often.
Decarburization
After melting in blast furnace, the pig iron contains about 4% carbon and some other substances from the ore, such as manganese or silicon. Branch iron is not malleable but must be freshened, ie the carbon content is lowered. The milling is done either by a well-iron method or a cast iron method. The modern large industry is based on the street iron methods. It is possible to melt the pig iron during oxygen supply in a fresh oven. During the 19th century, two important methods were developed that fresh iron in large quantities was the bessemer method and the martin method.
Bessemer
In Avesta ironworks, the little berry method was applied from 1878. In 1884, the berry mill was rebuilt and two new larger “Bergström's pots” were purchased. The method was used until 1901. The two Bessemer converters were placed next to the blast furnaces (1 and 2) and were charged with liquid pig iron.
The Bessemer process is the first for the production of liquid steel in large quantities. A bessemer converter is an iron container with a refractory coating. In the container, liquid pig iron is converted to steel by compressing air through the bath and the oxygen of the air burning the carbon of the iron. The product you got was called bessermerg.
The first converters in Avesta were small and filled with about 200 - 250 kg of pig iron directly from the blast furnaces. Due to the fact that slag followed, the fertilizer became poor. The later converters from 1884 were larger, about 1 ton, and gave a much better product. The Bessemer process was abandoned due to excessive burning (iron loss during blowing)
There are no bessemer converters left in Avesta.
(more to read in Folkarebyggden 1989,… ”Albert Bergström and his pots” by Otto Stjernquist)
Martin furnaces
In Avesta there have been six martin furnaces. The remaining ones are 2nd and 3rd.
In the martin furnaces, pig iron and scrap iron are melted during oxygen supply. During the process, additional substances were added which affected the properties of the iron. The product you received was called steel ingot.
Martin furnace no 2, the northernmost was erected in 1886-87. It was the first martin oven in Avesta. From the beginning it was a small oven that was filled, was charged with about 8 tons of iron. It was built from the beginning with acidic lining but was changed to basic in 1892. It has been rebuilt several times and had at the end basic lining and was charged with about 13-14 tons. It was used in the 1940s, according to a source until 1953
Martin furnace no 3, the southern one was built in 1895. The lining was basic. It was initially charged with about 7 tons of iron. This one has also been rebuilt and recharged at the end with about 13-14 tons and then had acidic lining. It was canceled in 1925 and has probably not been used since then. Drawings.
North of the 2nd was formerly No1 martin furnace. It was built in 1906 and was charged with 18 tonnes when it was demolished in 1954. The No1 replaced an older small oven from 1890 when it was built.
The charger that now stands at the 2nd is only used for the 1st. It is from 1916.
In sour martin furnace, hard steel or martingwood was produced. In basic martin furnace, soft iron was produced. The first martin furnace were sour. In the acidic process, the quartz brick is walled onto which a layer of powdered quartz is deposited. In the basic process, the hearth is walled of ordinary refractory brick and then a layer of magnesite gel, on which a hot mass of burned dolomite mixed with tar is evaporated. The additives during the course of the melt are then slightly different for acidic and basic processes.
A melting or "heat" varied in time. Acid melts took the most time about 7 - 12 hours. A basic melt went faster, about 6 to 8 hours, but even they could be for 10 hours if the melt stopped.
The Martin furnaces required constant maintenance, and therefore there were always masons who worked on maintenance and rebuilding of these. The furnaces were fired with gas produced using wood or coke in gas generators. Those who were responsible for the education were the parents. A work team at a martin oven consisted of a melter, an auxiliary melter, chillers and ladle meters
The ovens were heated with gas and air. Even heat gave good iron quality. From the regenerators, gas and air pass into separate channels until they flow into the furnace itself. Oven vaults and ducts are brick-walled.
In the upper part of the martin furnaces are the hearth. It is filled with pig iron, scrap and ore. The gas flows into the bottom of the furnace through the preheating chambers, up through hot grid-laid bricks into the hearth where the iron is melted. In the same way, air mixed with gas is preheated before it ignites in the oven room. The hot exhaust goes out into the other side of the furnace and down through its side preheating chamber where the bricks are heated by the exhaust gases. After a while, about 20 minutes, gas and air are released on this side and flow up to the hearth. The exhaust flows down to the first side preheating chambers. With interacting gas and air intake, the heat in the core increases to reach about 1700 ° C.
Oven 2 and 3 were charged by hand. A small locomotive ran into the carts with scrap. They came in through the tunnel next to the blower. See drawing. The locomotive drove the carts in front of them to the martin ovens. There, the scrap was taken directly from the wagons to the hearth. Long shovels hung in chains from the ceiling in front of the charging doors. The men filled the shovels by hand and then threw the scrap into the hearth with the shovel's help. Most things were filled in the first few hours. Later, under the melt, smaller amounts of ore could be added to speed up the melt. An acid furnace was filled most of the time before the oven was heated, but here too ore was gradually added to speed up the melt.
The melter sampled the melt in the oven and decided when it was time for bottling. The sample was first assessed for appearance but could also be tested in test equipment. The melter signaled that it was time for bottling. He then called on a small brass clock that hung on the gable of each furnace. The different ovens' clocks sounded different.
It took at least four men to knock holes for bottling. The men stood on the crane cart in front of the tap hole and hit the hole with a long spit. The knockout opening was clogged with a refractory stone surrounded by quartz mass. When the iron was to be dropped, the stone was buried and the iron then very quickly emerged. The melt was about 1700 ° C when it was ready. The men who hit holes protected themselves behind plates. When the melt came, it cracked and frowned. The drain hole was bricked again after bottling. The bottling of the steel took place in a large ladle held up by the crane trolley. The whole charge was lost at once, so the ladle must be so large that it holds the whole melt. The ladle had holes in the bottom for further bottling. The hole was closed using a lined iron bar, the rod. It was placed in a lever to be opened and closed. When the ladle was full, the rail trolley on the rails ran until the chill pit also called the measuring pit. The casting was made so that the steel ran through the bottom hole of the ladle into a "old man". At the bottom of the old man, there were masonry channels to the molds that were filled from the bottom. This was called casting. The molds could also be filled from the top, but it was more difficult to get good results. While the molds were being filled, aluminum pieces were thrown into the steel so that the steel would not coagulate. Drawing
Sometimes it happened a missed vintage, it was called a rush in popular language.
In all furnaces, there is slag. The slag from the martin furnaces was dropped into a pit. The product was called bumps and these were used as fillers or were driven away and left in the wild among the dead cases.
Ovens and other equipment were repaired and cleaned at about 3 - 4 months apart. Young little boys who worked at the ovens got to clean the gas pipes, crawl through them and suck them. The boys had a damp cloth as a mouthguard. The gases contained poisons so it was a dangerous work to crawl through the pipes. As a security, the boys were tied in a rope. If they were to tip off inside a pipe, they could be pulled out.
The workers had no special protective clothing, but there were their own blue shirts, trousers, wooden slippers and possibly protective gloves. Many worked without gloves. The huge radiant heat made the workers get leathery skin.
The Martin method was gradually replaced with electro-steel processes. The first electric furnace was started in 1922. It was engineer Otto Stålhane who designed the furnace. He constructed it as a variant of Rennerfelt's oven. In that furnace, the first stainless steel was manufactured in Avesta in 1924. Chargen had manufacturing number Y393 and this bottling number then became the name of the stainless steel product "AVESTA 393 ″. In the northern works, the electrostars were in the "lower martin", where there were also the 4th, 5th and 6th martins.
The crane
The crane was used to move the ladle from the 2nd and 3rd ridge gates to the chill excavators for bottling in the molds. As well as lifting up the molds when they were to be emptied.
The crane is a 6-ton double-arm swing crane made of steel and powered by an electric motor. The crane's lower arm, which supports the trolley, moves on rails in a circular motion. This is the second crane at this location. It dates back to 1907 and was used as long as these Martin furnaces were in operation. Before 1907, there was a swing crane powered by the foundry's turbine.
Cogging mill
The ingot that were obtained from the martin furnaces were rolled out to bars, substances, in the castings mill.
Verket is a duo roller mill with lifting table and return table. It was first turbine-driven but became electric-powered in 1949. It has a flywheel of about 6 meters in diameter. The old cogging mill consisted of three pairs of rolls and a universal rolling mill
The ingot was preheated in a soaking pit before rolling. There is no soaking pit left.
The blooming mill was commissioned in 1885 but was rebuilt in 1975. It was taken out of service…
The turbine for the blooming mill was constructed by C.A. Angstroms. The turbine was 2.2 m in diameter. It left a driving force of over 400 SEK. It was used from the start until 1949. ”According to Nils Rudberg, when the newly-used utility component in Avesta, this turbine collapsed in the spring of 1949 to the general consul's astonishment, as it has gone on at all times under all previous officers. It was replaced by a used electric motor from Hofors. ”(From the People's Buildings 1989, page 84, paragraph 14, text by Otto Stjernquist)
The blower machine
Blowing machine delivered air to blast furnace bessemer and martinverket.
It is a double acting piston blowing machine with a weather box. Originally it was turbine-driven but later powered by electricity.
Blåsverket was constructed and carried out at Bolinders mechanical workshop in Stockholm in 1884. The turbine was designed by C.A. Angstroms.
It was powered by electricity from 1917.
In 1884, a new wind power plant was needed when the old one was too small to "... serve it during the last year at Avesta's rebuilt berry-mill with two new Bergström's pots ...". "With a speed corresponding to 15 to 20 strokes of the machine, or an equal number of revolutions of the turbine, the proper blast compression is obtained from 0.87 to 1.06 kg.pr qvdm. Which is useful for the bessemer blowing. By using the aforementioned blast regulator, blisters are also taken out for the blast furnaces. ”(Engineering Association Negotiations 1884)
The first blowing machine was a Bagges that was set up for the river side
Further into the windshield room there are five fans that have been used for air for the martin plant.
Biography
printed:
A. Attman, Swedish iron and steel 1800-1914, Jernkontoret's mountain history series 21, Stockholm 1986
R. Andersson, Gamla Byn i Avesta, Dalarna's series of small papers, Falun 1976
H. S. Forssell, How ore becomes steel, Stockholm 1950
E. G: son, Odelstierna, Iron metallurgy, Stockholm 1913
K. Perers, H A Cornelius, from People of People's Buildings, Avesta 2001
O. Stjernqvist, Albert Bergström and his pots, from the People's Building in 1989
O. Stjernqvist, Avesta martinugnar, from the People's Buildings 1992
H. Tholander's set goals and heating system, from Jernkontoret's annals, year. 22
Swedish industrial works and facilities, 1919
Sweden's country and people, Stockholm 1901. IX Mountain management, Järiltproduktion by prof. J.G.
Wiborg
Double-acting twin-cylinder blower with turbine installed at Avesta mill, the Engineering Association's negotiations 1884
Turbine for the street mill at Avesta, the Engineering Association's negotiations 1888
Identification of the bearer Koppardalen in change, 2001
Unprinted:
W. Eriksson, Avesta Jernverk AB 1883 – 1964, part I and part II
B. Hermelin, Avesta Jernverk's blast furnace plant technical information, Avesta 1978
O. Widerström, The cabin facility at Avesta Ironworks, Swedish Mining Academy 1910
J. Wretlind, notes…on buildings, machinery etc. at Avesta Jernverk up to 1942
Recordings on minidisc and CD:
B. Sundberger, Interviews of people employed at the ironworks from the 1930s-40s
Archive material
Avesta municipal archives;
Drawings from Avesta Jernverk
Nordstjernan's central archive, Engelsberg;
Drawings from Avesta ironworks
Photos from Avesta Ironworks
Register of Avesta Jernverk's personnel 1884-1937
Personnel register, Avesta Jernverk 1908-1913 + 1925-1937
More to read
printed:
B. Hermelin, Avesta Jernverk and stainless steel, from Folkarebygden 1983
H. Kåks, Avesta industrial work and everyday life through 400 years, Falun 2002
S. Larsson and J. Saaving, Nordstjernan from within, Stockholm 1990
Nordic family book Owl edition. Several good references on iron handling
Newspaper articles:
the series "life at the mill", AT 96.12.24, 96.12.28, 96.12.31, 97.01.02, 97.01.04, 97.01.07
Night shift at the Martin plant, AT 85.02.19 (Fagersta)
Honorary Men, Metalworker 48.11.24
An enterprising Småland resident started the mill in Avesta, AT 99.12.03
Films about iron handling
Avesta Ironworks 1921, Av-centralen Avesta Municipality
Mixed film clips from Sandviken Ironworks, Culture Avesta, Avesta Municipality
This text released under cc-by-sa